Project Cargo Lashing Stages – Detailed Process, Techniques, and Application Steps
I. Introduction
Project cargo transportation involves the movement of oversized, heavy, and non-standard loads that require special lashing techniques to ensure safe transport. Proper lashing prevents cargo from shifting, toppling, or being damaged during transit. This article details the various stages of project cargo lashing, the techniques used, and key factors to consider.
II. Overview of Lashing Stages
The project cargo lashing process is a multi-stage procedure requiring meticulous planning and execution. The main stages include:
- Preparation Stage
- Equipment and Material Selection
- Load Placement and Balancing
- Lashing and Tensioning Application
- Testing, Inspection, and Documentation
III. Preparation Stage
A successful lashing operation begins with a thorough preparation phase.
- Assessment and Evaluation: The cargo’s weight, dimensions, and sensitivity are analyzed to determine the most suitable securing methods.
- Planning: A detailed operational plan is created, considering the required equipment, transportation route, environmental conditions, and safety measures.
- Work Area Preparation: The loading area is cleared and prepared, and safety measures are implemented before securing begins.
IV. Equipment and Material Selection
Selecting the right lashing equipment is critical to ensuring the cargo remains securely fastened throughout transport.
- Lashing Materials: Heavy-duty chains, steel cables, lashing straps, turnbuckles, and spreader bars are commonly used.
- Durability and Safety Standards: All equipment must comply with international safety standards. The load capacity and flexibility of the materials must be verified.
- Protective Elements: Edge protectors, rubber pads, and additional support elements are used to prevent cargo damage.
V. Load Placement and Balancing
Proper load placement is crucial for stable lashing.
- Weight Distribution and Balancing: The cargo must be positioned according to the vehicle’s center of gravity to prevent instability.
- Support Elements: Wooden blocks, steel braces, or modular stabilizers are used to reduce movement or tipping risks.
- Special Considerations: Fragile items such as glass or electronic components require extra securing techniques.
VI. Lashing and Tensioning Application
Once the equipment is set up, the cargo is secured through proper tensioning.
- Lashing Application: Straps, chains, and cables are placed strategically around the cargo to prevent movement.
- Tensioning and Locking: Turnbuckles and similar devices are used to apply and maintain appropriate tension.
- Even Tension Distribution: Equal tension is ensured across all securing points to prevent imbalances.
VII. Testing, Inspection, and Documentation
Once lashing is complete, final safety checks are conducted to verify stability.
- Final Inspections: All securing points, tension values, and cargo balance are rechecked.
- Testing Phase: Sensors and manual inspections ensure the cargo remains stable before and during transport.
- Documentation and Reporting: The entire lashing process is documented for compliance and review.
VIII. Conclusion
Project cargo lashing is a critical procedure that ensures the safe transport of heavy and oversized loads. Proper planning, the use of high-quality equipment, correct placement, and rigorous testing enhance transportation security. Future advancements in automation and smart technologies will further improve lashing efficiency and safety in logistics.
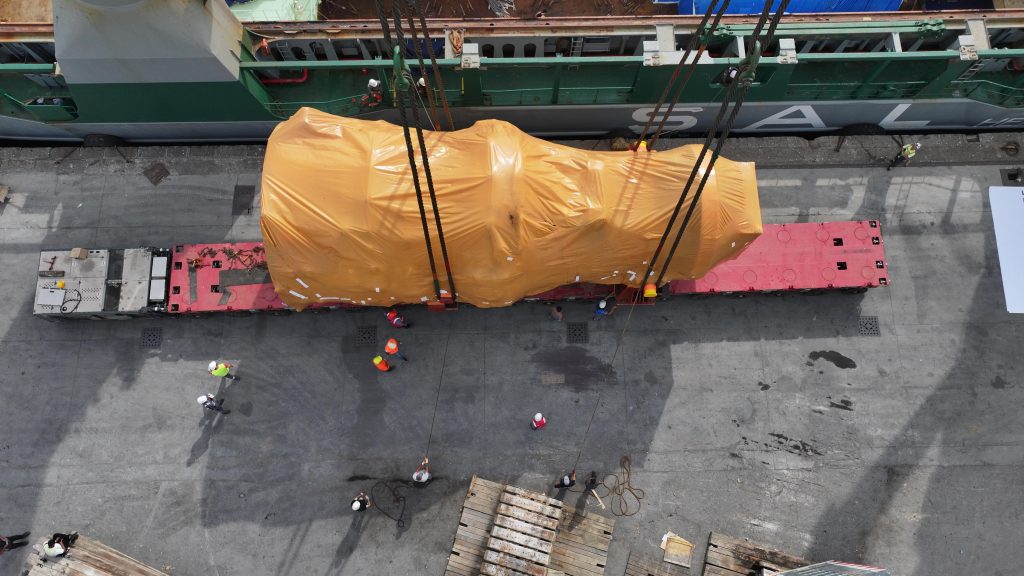
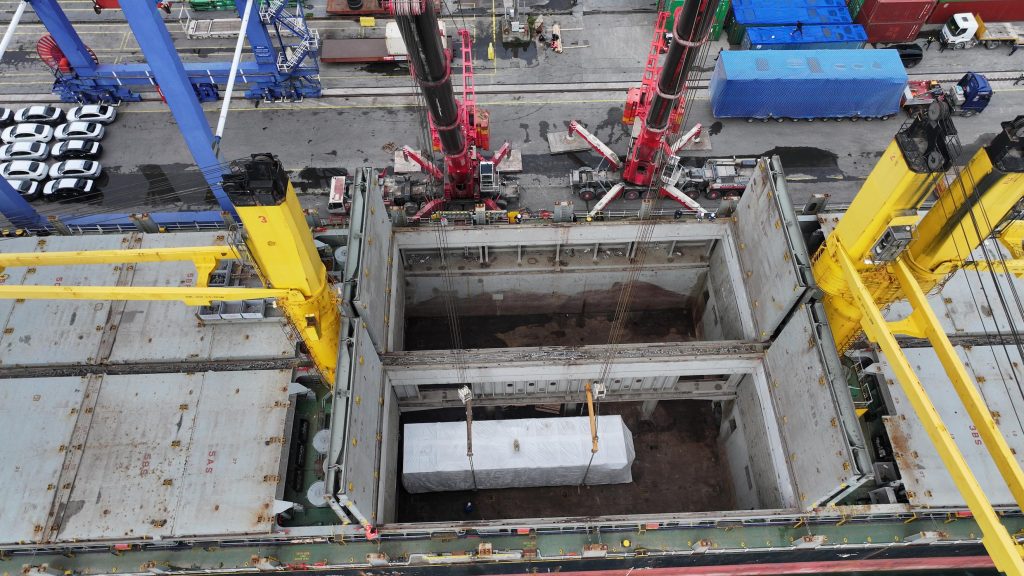
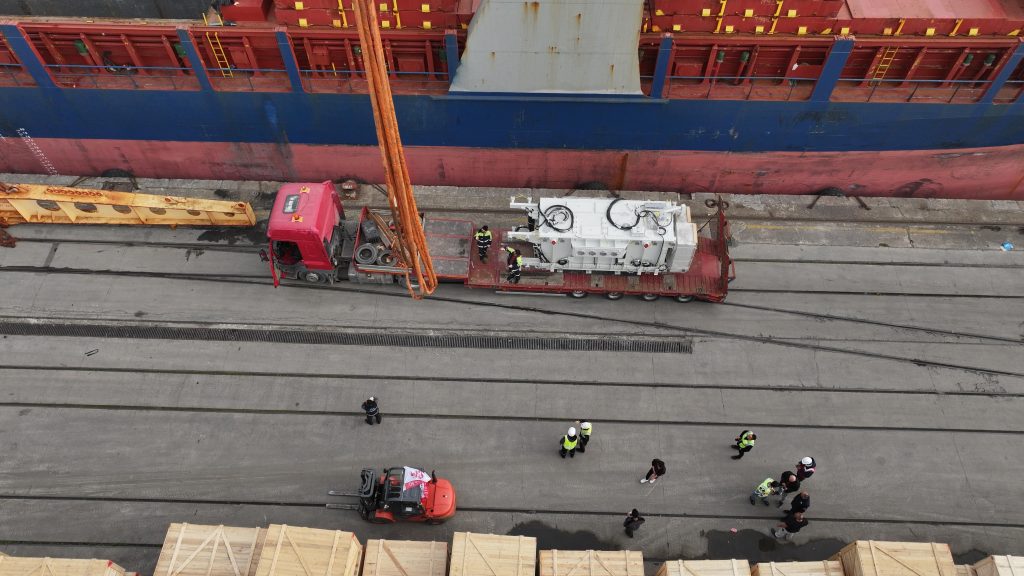